

"The result of an explosion in a plumber's van as a consequence of leaking gas cylinders"
|
|
The Testing of Gas Welding Equipment
Through the ProCus group of companies a comprehensive range of services are provided to industry. One of these many services is that of the testing of gas welding and cutting equipment, flashback arresters, regulators etc. Gas welding and cutting equipment now needs to meet a variety of Australian Standards and those standards may well be enforced by Workcover in the event of an incident. To conform to Australian Standards oxygen/acetylene regulators need to be refurbished or replaced every five (5) years and flashback arrestors, which are also recommended to be fitted to equipment, should be tested every twelve (12) months.
To ensure that your gas welding and cutting equipment is safe to use, many of ProCus’ representatives are certified to test and audit your equipment.
Welding Machine Repairs
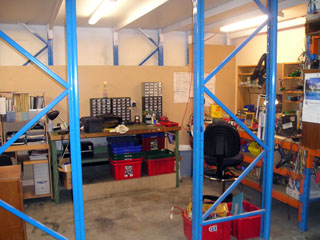
"Professionally equiped workshop".
|
|
To provide support for the welding machine products we import, as well being a recognized service agent for Australian manufactured welding machines, ProCus provides a welder repair service for a wide variety of machine types including MIG, TIG and inverter welding machines, as well as plasma cutters. Inverter welders represent electronics technology and therefore their repairs require the expertise of professionally trained electronics technicians. ProCus provides this welding machine repair service to our national clients and to the industry in general. On-site service is available, where practicable.
A welding machine hire service is also available.
Build-up and Repair of Shafts and Cylinders
"In-situ repairs to damaged hydraulic shaft"
|
 |
Another of the services provided for from within the group is that of the chemical metallising process. Representing Sifco of America this process enables the build-up and repairs to bearing surfaces on steel shafts, hydraulic shafts, printing cylinders etc. As the process can be provided as an on-site service, the process enables work to be done in-situ (on location) and often without equipment having to be dismantled. As the process enables a wide range of metals, including copper, nickel and chrome, to be deposited without heat, the problems of distortion are eliminated. Post machining can sometimes be rendered needless as metal can be deposited within tolerances. Thicknesses in metals of less that one (1) micron (0.00004”) can be deposited.
Overlaying of Ground Engaging Tools
"Tungsten overlayed compactor pads on a Caterpillar 825 Compactor".
|
 |
Years of experience in servicing the mining and earthmoving industries have provided an opportunity to extend the services we provide. Another of our companies, Tungsten Hardfacing, imports and overlays ground engaging and woodchipping tools with tungsten particle. These services are now being provided to the woodchip, mining, earthmoving and equipment hire industries. Equipment service life is substantially increased, therefore reducing operating costs and reducing equipment downtime. In addition to providing a quality tungsten overlaid product and a professional service, we also manufacture the applicators to apply the tungsten grit. This equipment encompasses the best technology available and can be readily purchased.
Engine Decarbonising Process
"On-site service for trucks and all diesel engines"
|
 |
Engine exhaust emissions are now a pre-eminent issue with most forms of diesel engine transportation, be it on a mine site or on the open road. We are all more conscious of our environment and the aim of all governments and the transport industries is to induce a reduction of diesel exhaust emissions. Our company, SmokeLess Diesel Service, is the Australian representative for MotorVac of America for its engine decarbonising process known as CarbonClean. An on-site service is provided and the process generally takes only between one (1) and two (2) hours to complete. The process encompasses the connection of the CarbonClean machine to the engine fuel line and the special diesel/solvent mixture is passed through the fuel pump and engine combustion areas. As the process progresses, residual carbon deposits are progressively softened and removed. The outcome results in a substantial reduction in particulate emissions and smoke and this is achieved without the need to remove the fuel pump or injectors. In practically all instances emissions will be reduced to conform to EPA requirements.
Decarbonising equipment available for purchase, rental and lease |